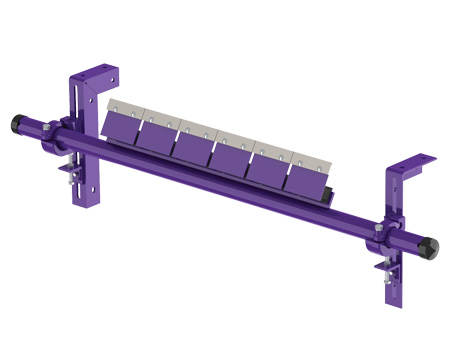
Industry
Steel
Application
Coke and Coal Handling
Product
H-Type® Segmented Blade Primary Cleaner
P-Type® Secondary Cleaner with
Corrosion-Resistant Tungsten Carbide Tips
Objective
Reduce belt cleaner blade wear
Extend product life span
Conveyor Details
Multiple belting types with speeds from 2m/s - 5m/s and widths from 800mm – 1800mm
Problem:
A high production steel plant in Southern New South Wales was experiencing faster than usual tungsten carbide tip wear on their primary and secondary belt cleaners. The plant has a production capacity of just over three million tonnes of steel per annum, meaning even a minor issue, like blade wear, could severely impact their production. Minimising any risk of downtime is critical to keep up with their high productivity. The standard tips would last 1-3 months and wear unevenly. The rapid wear was caused by an acidic compound from the quenching water used at the coke ovens, which would react with the binder in the tungsten carbide, causing them to become pitted.
Solution:
The site discussed their concerns with the rapid wear of the tungsten carbide tips to their Flexco Territory Manager. After a water sample analysis, the Flexco specialist concluded that there is a chemical reaction between the coked coal and the quenching water that is making the water corrosive and ultimately reacting with the binder in the tungsten carbide. To counteract this, corrosion-resistant tips were suggested to replace the existing standard tips on the belt cleaners. Over the past few years, the Flexco Australia team has researched, engineered, and manufactured a complete range of corrosion-resistant tips for abrasive applications. The tips are made from corrosion-resistant tungsten carbide and Stainless Steel 316, ensuring they quickly profile to the belt whilst remaining chemically resistant.
Result:
After replacing all primary and secondary belt cleaners with corrosionresistant tips, there was a significant increase in the wear life and cleaning efficiency of the tips. The blade life has now increased to 12+ months, more than four times longer than the standard tips. The site was so impressed with the results that they installed more belt cleaners with corrosionresistant tips in other areas of the plant. They now have a total of 30 belt cleaners with corrosion-resistant tips across their site.