Product Group: Endless Belt Splicing Systems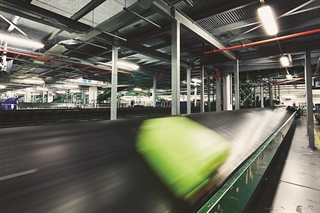
Product Line: Novitool® Aero® Splice Press & Novitool® Pun M™ Mobile Finger Punch
Industry: Airports
Application: Endless Belt Splicing
Product: Novitool® Aero® Splice Press & Novitool® Pun M™ Mobile Finger Punch
Objective:
Reduce Downtime
Reduce Maintenance Time
Increase Operator Safety
Conveyor Detail:
Belt Type: Solid Woven Black PVC COS
Belt Width: 47” (1.2m)
Belt Thickness: 1/8” (3mm)
PROBLEM
A major airport in Southeast Asia was constantly dissatisfied with their belt splicing capabilities. Not only was the third-party water-cooled press service they were using to splice their baggage handling conveyor systems expensive, but the results were often not truly seamless, leading to faster belt breakdowns. When yet another downtime incident occurred, they thought their only option was to continue using the outside service provider, so they made the call to schedule a repair. After splicing the damaged belt, the water-cooled system was having difficulty cooling down, eventually leading to a pipe burst, with hot water spraying towards their workers. The airport’s maintenance manager knew they were lucky to avoid serious injuries and decided that it was time to explore more options.
SOLUTION
To find the right solution for their facility, the maintenance manager invited several belt conveyor solution providers out for an in-house seminar where they explored what technology would work best for their application needs. Flexco’s solutions – the Novitool® Aero® Splice Press and Pun M™ Mobile Finger Punch – stood out from the crowd. After requesting a hands-on demonstration of the Aero Press with a Flexco Territory Manager, the plant’s management team noted just how quickly it was able to achieve a strong, endless splice, and was impressed by how repeatable the results were over the span of multiple demonstrations. Their team also liked how simple the Aero was to operate and knew it would be much easier and safer for first-time users. The fact that the Aero was significantly less heavy than the water-cooled press was also appealing, as having a portable unit would make splicing easier, especially if brought in-house. An added discovery during the demonstration was that the Pun M allowed their team to create fingers for belt preparation more safely for splicing, as they would no longer need to use an unstable utility knife that could potentially harm their workers.
RESULT
Two weeks after their seminar, the airport's baggage handling system was under immense stress as they were in the thick of holiday season. Unfortunately, a building fire broke out, damaging a line on their conveyor system, leading to downtime from three belt failures. Their maintenance team needed immediate relief, so they decided to call Flexco. Once a Territory Manager arrived, they were given a rough timeline of an hour-and-a-half to get their belts back in operation to avoid total disaster. Because of the portability and simplicity of splice recipe retrieval, the Flexco representative was able to bring the Aero directly to each repair spot and configure the splices with ease, completing all three in only 45 minutes. In turn, their conveyors were able to get back into operation, allowing bags to flow freely to their destination, avoiding the headache of dealing with lost and delayed baggage for travelers. This repair operation proved to be incredibly effective for their facility, leading them to invest in their own in-house Aero Press and Pun M units for future downtime incidents and recommending all local regional airports do the same.