The world of parcel handling and logistics has drastically changed in recent years.
From 2018 to 2022, sales figures essentially doubled. Across the globe, giants like Amazon and other third-party online retailers are selling, shipping, and moving more products.
Although this is great for these companies, the increased volume of packages is taking a toll on conveyor systems. Specifically, logistics facilities are seeing a sizable portion of their problems at their conveyor-to-conveyor transfer points.
From financial strain to system downtime, serious issues can creep up from an over-worked parcel handling system. See what problems can occur at conveyor belt transfer points and what you can do to stop them by reading more below.
Conveyor Belt System Transfer Pain Points
Consistently, the area that I see with the greatest opportunity for improvement in logistics facilities is at the conveyor transfer point. Both packages and the relationship with the customer are at risk when packages get lodged in the transfers. The packages might not reach their destination or may be damaged and the relationship with the customer could suffer.
The following are the biggest pain points I have seen at conveyor transfer points in my time as Flexco's Industry Manager.
Package Jams
The biggest issue found at transfer points is the volume of package jams. When a parcel or envelope interacts with an open conveyor transfer, it can become trapped between conveyors. In turn, the package can become damaged or destroyed.
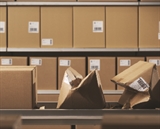
Not only does this cause financial strain in the form of reimbursement to the customer, but it can really hurt the relationship you have with them as well. In turn, they can refuse to do business with you in the future, negatively impacting your long-term profitability. How much money does it cost to reacquire a lost customer? (Hint: a lot!)
Belt Damage
Yes, a package jam can destroy the package itself, but that is only the start of the problem. When left unchecked, a package or parcel stuck in a conveyor transfer can break open. The contents can become lodged causing serious belt, and even structural, damage. This negatively impacts your entire belt conveying system, causing lengthy delays and costly repairs.
Product Loss
Another issue that I consistently see is lost packages at the transfer. Instead of simply becoming stuck between belts, a package can eventually dislodge itself, falling into a catch pan, net, or even to the ground below. How many shifts go by before that package lying on the floor or stuck in a catch pan is noticed and put back into the sortation system? And how much time do maintenance crews have to spend searching for and retrieving such packages?
There are also safety implications when packages fall through gaps to the floor below. This is of higher concern when conveyor systems are elevated overhead. I recently heard of a damaged box of high-quality kitchen knives opening and falling 25 feet to the floor, knife by knife, landing mere feet from a worker. Thankfully nobody was injured.
Featured Solution for Transfer Conveyors
The uptick of parcel handling in recent years has led to many exciting innovations for the logistics industry. To address the growing need for transfer solutions, the product development team at Flexco created our very own conveyor transfer plates.
Flexco Segmented Transfer Plates (STPs)
By quickly attaching to the side rails of the conveyor system, STPs sit flush in conveyor gaps, allowing for a good seal and smooth package transfers from one conveyor to the next.
And, with customizable installation options, STPs are ideal for virtually all logistics belt conveyors. After successful implementation, package jams, product amnesty and further system damage become a thing of the past. In just a few years, our Segmented Transfer Plates have proved to be incredibly useful for logistics facilities, with one major fulfillment center saving $1.8 million per day in downtime costs.
Other Conveyor Transfer Solutions
Yes, installing a product for smoother conveyor transfers is a great first step, but there are other Flexco solutions available to logistics site managers and their employees that help bolster productivity.
Learn More About STPs
Site Walkthroughs
To learn more about what Flexco solutions will work best, or to review and identify areas of your belt conveyor system needing immediate attention, it is worth setting some time aside for a site conveyor system walkthrough.
Site managers can connect with a Flexco Territory Manager to analyze their facility in person. While on-site, our industry experts will point out key problem areas, suggest proven solutions, and provide your team with real-world knowledge.
Request Site Walkthrough
Comprehensive Training Courses
Getting a hands-on feel for STPs can be incredibly beneficial for logistics site maintenance teams. At our two-day installation school, attendees get just that.
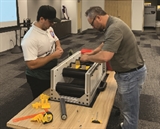
Joined by our team of product experts, visitors to our Walker, MI facility will learn how to conduct a thorough site evaluation, learn best installation practices on a lifelike training rig, and have the opportunity to ask questions and share their own experiences in an open, collaborative environment.
The Importance of Conveyor Transfer Solutions
All in all, those working in logistics and parcel handling know how crucial it is to have an optimized conveyor system. Addressing key problem areas like conveyor transfer points does not only save site managers from day-to-day headaches, but it further promotes a healthy financial bottom-line.
No matter what types of conveyor needs your business has, Flexco would love to be your partner in productivity.
Authored by: Todd Stewart, Industry Manager