The beginning of the summer holiday is a great time to discuss improvements being made in baggage handling and sortation systems along with challenges sortation systems will face, so in my newest blog, I would like to talk about trends and challenges in the industry now and in the future.
BELT CONVEYOR Updates, expansions, and technology
The expansion of the airport baggage handling industry is more exciting than ever and there is no sign of it slowing down. According to experts, massive updates and growth are expected through 2024. New airports and terminals are being planned or built, while existing terminals are being remodeled or upgraded to handle more passengers safely and effectively. And beyond the obvious infrastructure expense, there is ongoing investment into new technologies designed to improve baggage sortation and transfer accuracy on belt conveyors, as well as worker safety.
Radio Frequency Identification (RFID) technology is one of the newer technologies being widely adopted as airlines begin to install RFID chips into baggage tags. This technology allows the airlines to more accurately track where a RFID-tagged piece of baggage is at any moment in time. The new accuracy in tracking and tracing baggage travel is a big win for both travelers and airlines alike. I know I want to know where my bag is at all times, don’t you?
Baggage in a jam at conveyor transfers?
As older airport baggage handling conveyor systems are updated with new RFID baggage tracking technology, it will give airlines a better idea of where the issues are within any baggage handling and sortation system exist. With this technology, it is possible to locate the exact location of a piece of luggage tagged with an RFID tracking label.
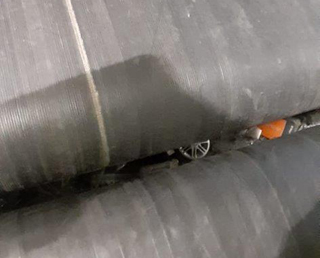 |
Baggage tags, straps, and wheels can easily get caught in open transfer points. |
One potential area of concern is at the conveyor-to-conveyor transfer points. It is common for bag straps, tags, or even wheels to become captured by ill-fitting transfer plates or in the gap between the conveyors when no transfer gap filler is used. When a piece of luggage becomes stuck at a transfer point, it can cause that bag to miss the connection to the aircraft, creating an unhappy customer along with a possible baggage damage reimbursement scenario for the airlines. In a worse-case scenario, the baggage piece lodged at a conveyor transfer could hold up other pieces of luggage, potentially creating an even larger quantity of bags to miss their connecting airplanes.
Another area that may put your bags in a jam are the screening conveyors. These systems process an excess of 600 pieces of luggage per hour and run at speeds close to 100 fpm (.5 mps), with multiple transfer points before and after the x-ray scanner tunnel. This mission-critical operation detects explosives, contraband and drugs in order to keep passengers safe. If a piece of luggage is trapped in between conveyors, it will clog the operation and minimize the effectiveness of the screening system.
Available airport conveyor solutions come in all shapes, sizes, and efficiencies
While the RFID tracking systems allow an earlier notification to baggage handling system managers of possible issues, this technology will not solve the root cause of the baggage jam.
A fully open conveyor transfer gap contains no transfer protection at all, straps, wheels or other items hanging from the baggage may get pulled down into the gap and become trapped between the head pulley and the finger/hand guard plate that is present as a safety precaution on many baggage handling conveyors. Again, a situation like this can cause a delay in the luggage making it through to the airplane and/or damage to the luggage itself.
Transfer plates (also called T-plates) are a good option to keep bags moving across the transfer points, bridging the gap and keeping items from getting damaged. But not all transfer plates are created equal.
Solutions such as steel transfer plates have drawbacks. Steel plates can work fairly well when installed properly. The issue is that steel transfer plates are extremely unforgiving and will hold onto lodged straps, tags, and other items, potentially causing damage to conveyed luggage or even to the conveyor belt itself. Speaking of the belt, any sort of damaged belting or belt splices can also catch on the static steel plate, causing further belt damage and requiring repair.
Engineered solutions work best at transfers
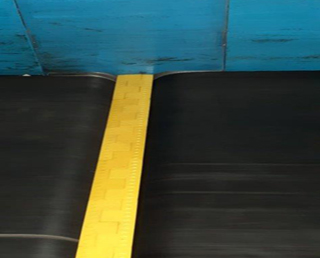 |
An engineered solution like Flexco’s Segmented Transfer Plate can keep bags moving and is easy to install and maintain. |
But do not fear. All is not lost. Flexco has developed a revolutionary new transfer plate system that is friendlier on baggage and conveyors alike. Flexco’s Segmented Transfer Plates are designed to allow safe and easy transfer of baggage and other conveyed items through conveyor transfer points. And in the unlikely event that a baggage strap or other item were to get lodged at the transfer, the 3 inch (75mm) wide, high-visibility yellow segment would simply lift out of the way or release completely. This frees up the jam, leaves transfers protected, and discourages conveyor belt damage.
If a segment did release from the support bar, a repair can be made in a matter of seconds by simply snapping a new segment into place. Even better, replacement segments are easily inventoried by the baggage system maintenance crew. No more custom-fitting of steel transfer plates or other homemade transfer gap filling solutions.
If it ain’t broke...
You may not have even realized that your transfer points were that big of a problem when it comes to your entire operation, and you still may read this blog and think that it’s a nice idea, but that you and your crew don’t have time. But let me ask this, “Do you have time to increase your efficiency and decrease your mishandled baggage claims?” I think we all can find time for that.
Stewart has been with Flexco for 30 years, working in various roles from customer service, to manufacturing, to training and new product development. As Industry Manager, Stewart thoroughly researches target industries, creating programs to support each industry and identifying customer issues, as well as potential product solutions. Stewart currently leads the development of the Parcel Handling Industry Program and is responsible for ensuring that Flexco is positioned to serve the needs of our global customers. Stewart earned a bachelor’s degree in Marketing with a B2B specialty from Davenport University.